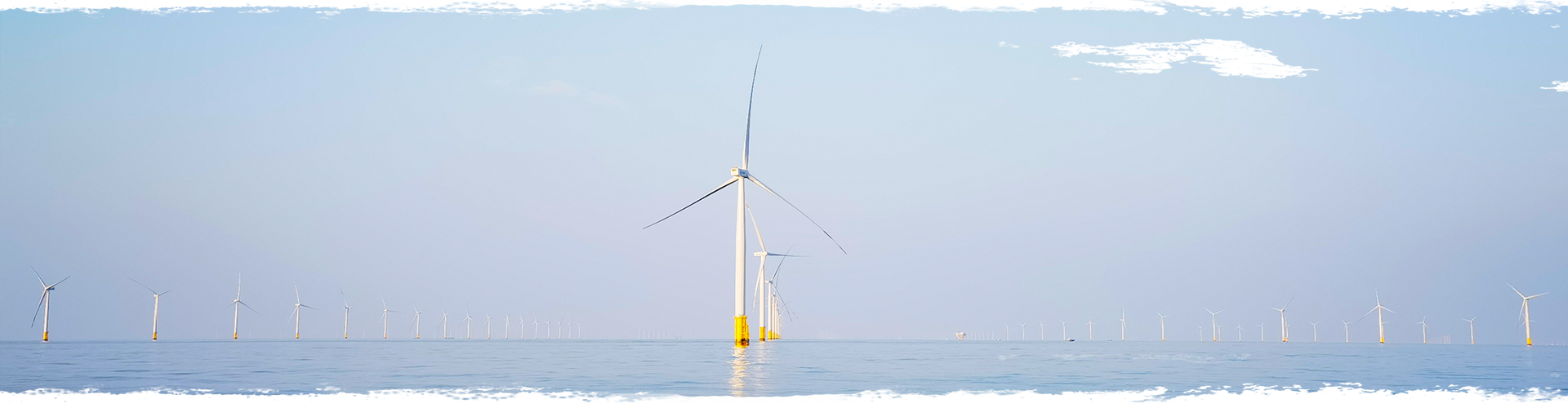
在长江入海口,“海峰1001”2500吨自航自升式风电安装平台整装待发。这艘风电安装领域的“国之利器”长133.8米,型宽50米,型深11米,由中交海峰风电发展股份有限公司投资研发、上海振华重工(集团)股份有限公司制造,能够满足深远海一体化海上风电施工作业需求,大幅提升了我国海上风电施工作业能力。
力拔千钧的“海上巨无霸”
面对海上风电深远化、机组大型化的发展趋势,“海峰1001”风电安装平台深度融合中交集团在深远海核心装备研发方面的资源优势与施工经验,采用差异化设计方案,最大作业水深可达70米,桩腿总长120米,主要突出船舶的起重能力,兼顾打桩功能,适用于国内沿海风场砂性土、粘性土及类似地质作业。
平台上的新一代绕桩式起重机采用剖分式三排圆柱滚子组合转盘轴承,名义直径达到14.688米,是国内目前最大直径的剖分式回转轴承,具有结构紧凑、承载能力强、运行平稳等优点,极大优化了结构形式,实现了2500T的起重能力,是目前国内平台安装起重能力最大的起重机。实现了2500吨目前国内最大起重能力。
从2022年5月16日开工至今,“海峰1001”按计划完成了进坞合拢、主船体贯通、吉水、试航等重大节点,克服了技术质量要求高、施工组织复杂、交叉作业多、有效作业窗口时间少等重重困难。
“在300多个日夜里,项目团队市场调研了国内外风电安装船的性能参数,先后进行了50多次的技术攻关,110余次的讨论交流,最终设计出满足深远海、大容量、一体化施工作业要求的安装平台,使甲板可变载荷达到6500吨,可一次性运载2套20兆瓦风机机组设备。”回忆起建设历程,项目负责人黄超心潮澎湃。
作为国内自主设计研发的第四代海上风电安装平台,“海峰1001”能够在海况复杂的深远海域,依靠稳定性强、定位精度高的DP-2动力定位系统进行航行和定位。为了驱动这艘“海上巨无霸”,平台在艉部设置3台3000千瓦全回转推进器,艏部设置3台2500千瓦艏侧推。同时,为满足大容量风机的吊装需求,右舷设置2500吨绕桩式全回转起重机和380吨辅起重机。
“力拔山兮气盖世”,2500吨的起重能力,标志着我国大型海上风电施工船舶制造能力和关键核心技术实现重要突破。中交海峰风电联合振华重工,以打造“世界一流的国之重器”为目标,在知识产权方面完成了《深远海自升自航式风电安装船的研制与应用》科技课题研发和《一种风电安装平台船的可拆卸风机叶片搁架》等10余项专利。
智能运行的“深海电梯”
海上风高浪急,如何使船舶在作业过程当中保持平稳运行?
项目负责人黄超介绍,海底地质条件复杂,但“海峰1001”上的4个桁架式桩腿,能够像“定海神针”一样插入深淤泥海底层,使
平台船体在海上牢牢站立,不受海浪影响,确保施工如履平地。
“齿轮齿条式升降系统是整个平台上最核心的部分,就像电梯一样,在海上能够平稳地进行平台的上升和下降。系统由144个抬升单元组成,每个抬升单元能承受200多吨的重量,从而能够在海上将重量为28000吨的船体抬离海面,形成一个稳定的工作界面。”项目负责人黄超解释。
走进位于船上的中控室,中控屏上正在显示从升降系统上布置的各种传感器收集而来的数据。系统通过变频器“一拖一”的对抬升电机进行载荷的动态调整和自动均分,从而实现“深海电梯”的平稳上升和下降。
除了超强的起重能力和高效平稳的升降系统,信息化和智能化是“海峰1001”的又一亮点。通过全船信息化数字化管理平台,管理人员在岸上就能对海上运营船舶进行远程监控、远程诊断和远程运维,实现船舶与岸基的高效无缝对接。
“‘海峰1001’是国内首艘申请CCS智能船舶(I-ship)及绿色船舶(G-ECO)入级的海上风电安装平台,升降系统、起重机和桩腿桩靴三个核心配套装备均实现国产化应用,通过信息化系统实现远程‘监测+诊断+运维’一体化能力。”项目负责人黄超说。
在装备研发的过程中,中交海峰风电精准定位市场需求,不断追求装备智造与技术突破,形成《海上风电安装船舶管理信息化系统》、《一种自升式风电安装船的桩靴冲桩结构》等专利。该专利在平台船插拔桩适应性研究及冲桩系统方案优化方面具有创新性和新颖性。
在“双碳”目标指引下,全球能源革命正在加速推进,海上风电成为我国能源转型的重要抓手。“海峰1001”2500吨自航自升式风电安装平台的投入与运营,将提升中国在全球海上风电领域的竞争力,为中国海上风电的可持续发展做出重要贡献。未来,中交海峰风电将继续与产业链伙伴携手并行,在中交集团支持下打造海上风电全产业链,不断刷新中国在海上风电研发设计与高端制造领域的记录!(图片由朱云龙授权提供)
来源:中国日报网
上一篇: 全球最大海上风电场首次发电
下一篇: 为什么海上风电技术是实现净零排放的关键?