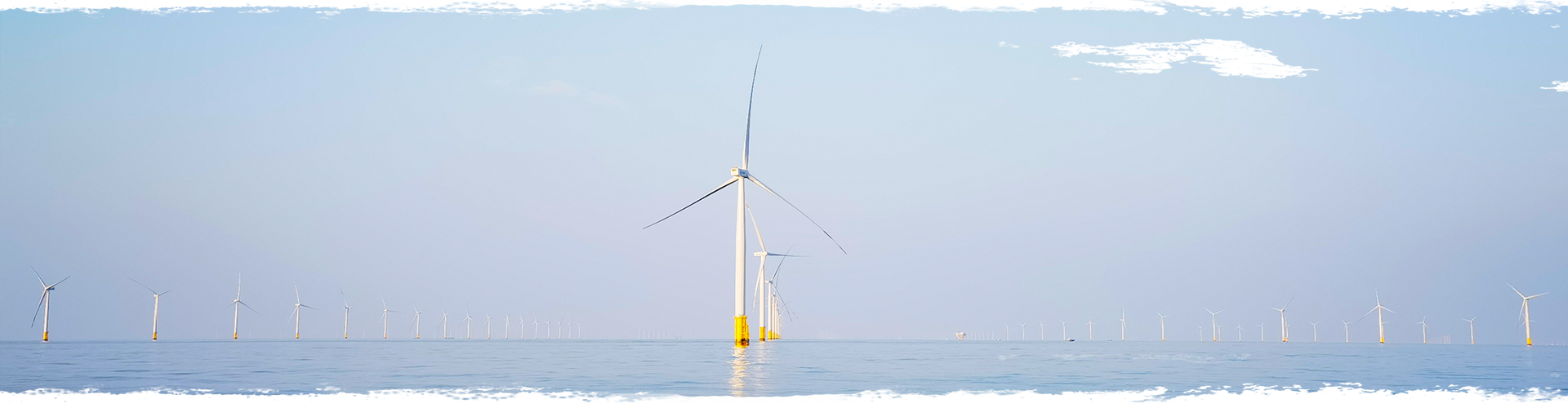
编者按
管道输送是经济高效的CO2运输方式,海洋CO2运输是离岸碳捕集、利用与封存(CCUS)产业链的关键环节和规模化开展离岸CCUS工程建设所需的核心技术。我国正在不断提升海洋CO2管道输送的工程与技术,为实现碳达峰、碳中和战略目标而努力。
中国工程院院刊《中国工程科学》2024年第2期刊发厦门大学材料学院王子明副教授等人的《海洋CO2管道输送技术现状与展望》一文。文章明晰了我国实施离岸CCUS的优势、典型海洋碳运输情境和海洋CO2运输方式,剖析了国内外海洋CO2管道输送的技术与工程概况;从CO2流体相态及流动安全,沿程腐蚀风险估、监测及预警,CO2泄漏实时监测技术,高压CO2泄放及对环境的影响等方面梳理了海洋CO2管道输送工艺技术现状;从CO2管道材料断裂行为及止裂措施耐蚀及密封材料、碳钢管道长寿命运行的关键腐蚀控制技术、注采井筒的腐蚀风险评估等方面梳理了海洋CO2管道材料技术现状。研究认为,加快发展适应海洋CO2管道输送复杂工况的材料体系、全流程CO2管道的智慧管理与数字孪生技术、海底CO2管道全生命周期运行关键技术、在役海底管道改输评估与保障技术,采取加快推动我国近海碳封存CO2管网规划、拓展和深化跨行业 / 跨机构合作模式创新、系统建设海陆统筹的标准体系、引导专业化技术服务企业深度参与海底CO2管网建设等举措,促进我国海洋CO2管道输送体系高质量建设。
一、前言
碳捕集、利用与封存(CCUS)正逐渐发展成为我国实现碳达峰、碳中和(“双碳”)战略目标的高效解决方案之一,涵盖捕集高浓度工业产生CO2、加压后集中运输至目标区块、进行价值利用或地质封存在内的完整技术链。早在20世纪70年代,北美地区即探索利用CO2提高石油采收率,在应用中实现CO2动态地质封存。在我国,吉林油田、胜利油田等油气开发企业较早启动了CO2驱油利用与地质封存的规模化工业试验,初步形成了陆上CCUS工程的全流程技术链。2023年7月,我国陆上首条年输送量超百万吨的中国石化齐鲁石化公司—中国石化胜利油田CO2管道顺利建成,主体部分长度为109 km,将中国石化齐鲁石化公司工业废气中的CO2捕集、纯化、增压后经管道输送至中国石化胜利油田纯梁采油厂进行驱油利用和地质封存。这一项目的投产,标志着我国陆上CCUS工程步入了商业运营阶段。
相较陆上CCUS工程,我国离岸CCUS工程起步较晚。2021年,中国海洋石油集团有限公司启动了我国首个海上CO2封存示范工程(恩平15-1油田),工程于2023年建成投运,每年将约3×105 t来源于中海油恩平油田群采出气分离的CO2注入海底800 m深的封闭咸水空间并永久封存。同期,我国在渤海、东海、南海等海域开展了多个海洋CO2封存的前期可行性研究。源自北欧地区的离岸CCUS工程经验表明,在低碳经济指标的引导下,海底广阔的地层空间可能是未来大规模封存CO2的最佳场所。
随着离岸CCUS项目的发展和深化,高效匹配CO2产生源与CO2封存有利区成为工程实践中的一大难题,又以安全且低成本的海洋CO2运输作为重点考量因素。本文针对我国发展离岸CCUS产业链面临的CO2运输问题,从海底碳封存的工程需求出发,立足海洋CO2运输方式、海洋CO2管道工程现状,力求全面梳理海洋CO2管道输送涉及的材料、工艺等要点,辨识相应技术瓶颈并总结发展方向,为加快离岸CCUS技术体系建设、推进离岸CCUS工程应用提供基础参考。
二、离岸CCUS工程发展背景
(一) 实施离岸CCUS的优势
近年来,沿海各省份积极发布有关可持续海洋“蓝色”经济的政策,使离岸CCUS得到越来越多的关注。建设离岸CCUS工程,将显著拓展碳封存空间,为实现“碳中和”目标提供更多选择方案;有助于多元化利用海洋能源资源,助力海洋经济发展。我国开展离岸CCUS工程建设,具有以下三方面优势。
1. 海底碳封存潜力及源汇匹配
我国海岸线总长度超过1.8×104 km,近海海域面积超过4.7×106 km2,相应的海域CO2地质封存潜力为2.58×1012 t ,可为实现“双碳”目标提供重要支撑。东部沿海地区是经济发达地区,具有大量的工业碳源(约占全国碳排放总量的41%),可与海洋地质碳汇空间进行高效的源汇匹配。我国离岸50~300 km范围内的近海沉积盆地,有着巨大的CO2封存容量,可以满足沿海地区百年以上的碳封存需求。
2. 封存安全与风险可控
对于陆上CCUS,即使在向地层注入CO2前执行了严格的选址标准、采取了周密的方案设计,在注入过程中及注入后依然需要考虑CO2泄漏的潜在风险。相比之下,离岸CCUS工程风险的后果更小,这是因为:海底环境因海水压力的作用而较陆上环境更不利于CO2的规模化泄漏;海水的溶解、扩散等过程可极大降低海洋CO2泄漏带来的环境影响;近海海底封存远离人口聚集区,CO2泄漏造成的经济社会后果相对可控。
3. 海洋能源协同利用与开发
我国近海海洋油气资源丰富,如东海、南海区域的石油储量预计值分别为1×1010 t、2.75×1010 t 。联合实施海底碳封存、CO2驱油,能够以经济的方式实现油气领域“双碳”目标,甚至能够实现“负碳排放”的油气开发模式。此外,充分发挥海上风电、潮汐能、波浪能等能源资源,能够进一步优化离岸CCUS产业链,降低CO2捕集、运输、利用等方面的成本,从而推动传统行业与新能源产业的融合发展。
(二) 典型的海洋碳运输情境
在离岸CCUS工程中,从碳源规模、海洋封存选址角度看,存在3种典型的碳运输模式(见图1):陆‒海运输、海‒海运输、跨区域远距离运输。
图1 典型海洋CO2运输模式
陆‒海运输模式具有规模大、连续产出的特点,碳源多为沿海热电厂、化工厂等捕集的燃烧后CO2,经纯化后仍含有少量水汽、氧气以及硫氧化物、氮氧化物等杂质组分。该运输模式涉及各类工厂产生的CO2汇集至沿海CO2储运点、通过大规模长距离的海上运输到达封存点。
海‒海运输模式中的CO2主要是海洋油气生产过程中分离的燃烧前CO2,通常含有少量水汽以及H2S、烷烃等还原性气体。该运输模式需将各生产平台或海底工厂分离出的CO2运输至集中平台进行增压注入,以实现海洋平台之间的碳转运。
跨区域远距离运输模式指跨省份、跨地区甚至跨国、跨洲际碳交易情形下的海洋CO2运输,碳源呈现多样化,通过较远距离(>500 km)碳运输到达最优的海底碳封存地点。相应运输线路可能途经陆地、海洋等,运载量主要与碳源量、碳税政策、经济指标等因素相关。
(三) 海洋CO2运输方式
海洋CO2通常采用的输送方式有水上运载器(如船舶)、水下管道等。在海洋碳运输方式的决策中,运输成本是重要影响因素之一,需兼顾碳源形式、输送量、输送距离等变量进行优选。船舶运输适用于:小规模、分散碳源,水路运输线路密集分布的地区;跨越区域较远距离的碳运输。管道运输具有规模大、运量稳定等优点,是陆地或海洋CO2连续大规模输送的备选方案,适用于碳源稳定、输量大、距离适中的海 / 陆碳封存工程。当前的CO2管道主要建于陆上,如北美地区建设的CO2管道长度累计超过6000 km。海洋CO2管道工程案例较少,挪威Snøhvit项目是目前规模较大的海洋CO2管道工程。欧洲规划的CO2管道建设里程为3×104~1.5×105 km,多为海底管道。鉴于我国沿海地区的碳源与碳汇格局,未来一定时期内我国海洋CO2管道输送的需求量巨大。
从工程投资的角度看,船舶运输、管道运输在大规模CO2输送方面均具有优势,如运载量超过1×106 t/a后,对于250 km运输距离,可将运输成本控制在1~10欧元/t的较低水平。我国陆上CO2管道的运输成本可低至0.4~0.6元/(t·km),海洋CO2管道的运输成本通常为同等规模陆上方案的2倍,主要原因是后者的建造成本高出40%~70%。船舶运输是间歇性流程,运输船的系泊受海洋环境影响较大,需要设置大容量CO2储罐,都将增加船舶运输成本。海洋运输方式的选择通常取决于运载量和运输距离。在固定年运量的条件下,海底管道在短距离运输时更经济。我国海洋CO2管道将呈规模化发展势头,相应的单位运输成本走低,在远距离运输中也将逐渐取代传统的船舶运输。
三、海洋CO2管道输送的工程与技术现状
(一) 国外海洋CO2输送工程案例
1. 陆‒海远距离输送与注入
挪威Snøhvit项目是目前少数成功运行的海洋CO2管道输送项目,自2008年开始运营,将Snøhvit液化天然气工厂捕集的CO2运送至153 km外、300 m水深的海底碳封存点,设计输送量约为7×105 t/a。Snøhvit气田的天然气中含4%~9%的CO2,在处理站场经过捕集和纯化后,再采用分子筛技术将含水量降至极低水平(摩尔比为5×10-5),以最大程度控制运行过程中的管道腐蚀风险。管道入口端的CO2流体温度为25 ℃、压力为15 MPa,输送至海底管道末端后温度降低至5 ℃。海底管道全程焊接(不分段),未设置中转站或增压站、阀门等设施,仅在陆地段设置管道清扫设施用于特殊工况下的应急处置。基于动态生产模拟软件进行管道运行的全程实时监控,辅助进行泄漏探查、清管器模拟跟踪和自动控制。
2. 海‒海近距离直接注入
Sleipner项目位于挪威北海区域,是国际上最早开展海上CO2封存的项目;CO2分离自海上生产的天然气,被注入至临近天然气藏(深度约为1000 m)的地质储层内。注入系统位于天然气生产平台,故无需长距离输送CO2,CO2被分离后未经干燥流程直接加压注入地层(注入压力为6 MPa、注入温度为25 ℃);采用25Cr不锈钢管道以抵御腐蚀问题。项目自1996年开始运行,累计注入CO2约2.7×107 t ,注入管道未发生腐蚀和泄漏情况,验证了高耐蚀材料在短距离输注工况中的应用可靠性。
巴西Lula油田是国际上首个开展离岸大规模CO2驱油工程的油田,2011年正式启动,工程水深约2200 m,采用浮式平台开采模式以提高经济性。为提高石油采收率和环境效益,将伴生气中的CO2(含量约为12%)直接在采油平台进行分离和回注,无需长距离输送,在生产区设置1组CO2注入井、2组气水交替注入井。经多年运行后,注入井处未发生明显的水合物、结垢、流动安全等问题。
(二) 我国海底管道技术发展现状
我国基本掌握了海底管道铺设、耐蚀管材研制、海底管道检测评估、海底管道维修等关键技术,为海洋CO2管道输送工程建设提供了坚实的技术支撑。
1. 海底管道铺设技术
过去20年,我国海底管道铺设能力得到跨越式发展,作业深度从浅水逐步走向深水,具备1500 m深水油气管道的自主建设能力。在海底管道铺设装备方面,拥有S型、卷筒铺设等铺管船,柔性管道铺管船、水下机器人、喷射式和犁式挖沟机等海底管道工程大型作业装备。2019年,在东方13-2油气田自主建成了铺设最长的海底管道(长度为195 km、管径为0.6 m)。在深海作业能力方面,2021年“深海一号”气田建成我国最大水深的海底管道(长度为4.5 km、管径为0.2 m),最大作业水深达1542 m。
2. 海底管道新材料技术
我国海底油气管道普遍采用X65材质。南海荔湾输气管道工程采用了X70材质,管径 / 厚度比为24.1,总长度为160 km,是高强度等级钢材用于海底管道的最新案例。近年来,相关机构加快开展高强度、大厚度管材的研发与应用,整体技术水逐步接近国际先进。在酸性等腐蚀介质环境中,新型耐蚀材料开始用于海底油气管道,低成本、高耐蚀的双金属复合管在深海油气集输方向具有广阔的应用前景。2017年,我国首次在文昌油田自主铺设总长度为4.92 km的不锈钢复合双层海管。具备超深水工况下柔性管的自主安装设计和施工能力,掌握垂直铺设作业关键装备技术,已在流花油田、陵水气田等区块形成工程案例。然而,高性能热塑性管材及相应的多层复合界面增强技术仍待攻克,才能推动海洋柔性管的规模化应用。
3. 海底管道检测评估技术
海底管道在运行过程中,受到机械或化学作用可能导致局部破裂而引发不同程度的泄漏。现有的海底管道检测评估技术可分为预防性检测技术、泄漏定位技术:前者侧重于评估管道破坏风险,如保温层完整性,管道内壁腐蚀产物、腐蚀速率、含水率的在线监测信息;后者属于事故感知型监测手段,用于实时或在短时间内判断泄漏发生位置,以负压波、次声波等监测分析方法为代表。在具体实施过程中,通常需要多种技术手段联合运用才能准确定位事故。
4. 海底管道维修技术
海底管道维修从空间上可分为水上维修、水下维修:前者借助重型支持船进行海上提管维修或修补作业,适用于浅海区域中等以上破损的海底管道(需要管道停输);后者直接在海底对破损管道进行更换维修或开分支等作业。当管道局部损伤时,可采用不停输封堵维修技术,如夹具或管卡维修、机械式三通维修法等;当管道严重损伤或断裂时,需在停输状态下借助机械连接器进行修复或者采用水下焊接进行维修。借助干式舱开展水下焊接仅适用于水深30 m以内的浅水区,更深海域工况需要发展湿式水下焊接技术。
(三) 我国在役海底管道工程现状
当前,我国海底管道总里程超过9000 km,其中油气混输管道、天然气管道、注水管道、原油管道的占比分别为40%、19%、26%、13%,尚无用于CO2输送的长距离海底管道。我国海底管道多为新建工程,服役时间少于10 a的管道占比约为57%,服役时间超过25 a的老旧管道仅占8%。海底管道的建设成本高昂,因而挖掘在役管网的调配潜力、进行多种介质分批次或定期转输是未来的关注点。目前,我国已有开展海底管道转输的工程案例,如渤海BZ34-1油田实施了22 d的海底天然气管道改输原油方案,在海底输水管道转输油气混合介质、含腐蚀缺陷的输水管道转输天然气等方面也开展了探索,为后续的在役海底管道转输CO2提供了技术借鉴。天然气管道设计压力一般高于10 MPa(如荔湾海底输气管道设计压力高达23.6 MPa),能够满足转输密相CO2的压力等级要求;原油或油水混输管道设计压力多数不高于8 MPa,仅适用于气态CO2输送。
四、海洋CO2管道输送工艺技术及面临的挑战
(一) CO2流体相态及流动安全
海底管道内CO2以气态、液态、超临界态、固态等多种相态形式存在,决定了管道内流体的流动特征。杂质气体会改变CO2流体的黏度、密度、相区以及临界相转变点,进而影响输送效率和流动安全。在海底管道的低温、高压服役环境中,微量水可能促使CO2水合物析出,成为影响管道流动安全的重要因素。
1. CO2流体相态
CO2相态取决于管道输送的温度和压力。在海洋环境中,如不采取高效保温措施或辅以伴热系统,长距离运输过程中管道流体温度将接近于海水温度。按照理论模型,起始温度为15 ℃的CO2流体在输送1.5 h后,其温度下降至5 ℃左右;这一预测温变与Snøhvit项目实际管道温度的演变规律相符。管道内流体压力的变化与海床深度、输送距离相关,在CO2自重作用下管道流体压力逐渐增加,而远距离管道输送会降低压力。在Snøhvit项目中,管道入口端的压力为15 MPa(设计压力为21 MPa),153 km外、300 m深的海底井口处压力仍为15 MPa,表明CO2重力压差与管道压降相等。
图2展示了海底管道中CO2相态随温度和压力变化的典型演变路径。CO2处于超临界态时,因其具有高密度、低黏度的特点而被视为陆上管道最高效的CO2输送状态。美国Cortez项目中即采用超临界态CO2(压力为9.6 MPa、温度为43 ℃)进行输送。采用超临界态CO2输送时,全线运行压力应高于1.1倍的临界压力(即8.1 MPa),以避免压力波动而进入CO2气相区间。在英国Longannet、Kingsnorth项目的前端工程设计报告中,示范阶段、全规模阶段分别采用了气相输送、高压密相输送的设计方案。采用气相输送方案具有压力低、成本低的优势。对于海底管道,建议采用液相输送。
图2 海底管道中CO2相态演变路径示意图
在长距离输送过程中,CO2随着温度下降、压力增加而保持单一液相;在注入井筒内被地温加热后,1000 m左右深度,CO2流体开始转变为超临界态,密度不会发生突变,对井筒运行安全的影响较小。然而,在管道试运行、故障停运、压力泄放或停输再启动等过程中,控制管道压力显得尤为重要,因为频繁且高载荷的压力波冲击可能导致海底管道固定系统损伤以致出现大幅度位移。
2. 杂质气体对CO2流体的影响
由于碳源和捕集方法的差异,CO2流体中含有不同类型的杂质气体,如燃烧后工艺捕集的CO2中含有一定量的N2、O2、CO、SO2、NO2等,天然气中直接分离的CO2中往往含有一定量的CH4、H2S、H2等。当杂质气体含量达到工程上限时,将对CO2流体的诸多物理参量产生影响(见图3)。① 杂质气体对CO2密度的影响取决于其分子量,较大分子量的气体趋向于增加CO2密度。② CO2流体黏度与分子间的摩擦力,和杂质气体导致的紊流有关。SO2、H2S、H2O的存在将提高CO2流体黏度,从而增加管道输送能耗。对于密相输送的CO2流体,其黏度随温度升高而降低。③ 在水平管道内,较CO2轻的杂质气体会提高流体流速,导致管道摩阻增加、管道压降加大;仅有SO2、H2O会缓解沿程压降。在下坡管道内,受流体重力的影响,较CO2重的杂质气体将进一步增加流体压力。④ 杂质气体导致CO2分压降低,可能进入气液两相区。H2、N2将导致最宽的两相区范围,而H2O、H2S几乎不改变CO2的相区分布。⑤ 各种杂质气体均会提高CO2的临界压力(即>7.37 MPa),较高的临界压力预示着CO2流体需在更高压力下才能维持密相输送。SO2、H2S、NH3可提高CO2的临界温度,其他杂质气体均可降低CO2的临界温度。提高临界温度有利于CO2流体保持密相输送的安全性。
图3 杂质气体对CO2流体性质的影响程度
从图3可知,N2对CO2流体行为的影响较为明显,而H2S的影响较为微弱,该结论对工程实践具有指导意义。在进行地质封存时,对海上天然气分离的CO2中H2S含量上限可不作要求,而燃煤电厂等燃烧后捕集的CO2输送时,合理控制N2含量成为保持流动安全性的重要手段。
3. CO2水合物的形成及预防
CO2水合物是由CO2分子、水分子按特定比例构成的笼合物固体结构,若聚集会堵塞管道和阀门并影响设备运行。当存在游离水时,只要流体温度和压力位于水合物形成区(见图2),便会形成一定体积的CO2水合物。低温、高压的海底管道输送环境有利于形成CO2水合物。CO2水合物形成与液态CO2中水的溶解度极限相关,快速降温可能导致CO2水合物析出。例如,在压力为8.89 MPa、温度为-5 ℃时,摩尔比为0.001 1的含水量不会导致CO2水合物析出;当温度降低至-10 ℃,将会析出少量的CO2水合物。在稳态输送工况下,只要严格控制CO2流体的含水量,即可避免水合物析出。在北美地区Weyburn、NJED陆上CO2输送项目中,采用了较低的含水量(摩尔比分别为5×10-5、4.18×10-4),即使在冬季低温环境中管道内也未发现CO2水合物。当含水量较低时,即使启停过程中或偶遇温压突变导致CO2水合物析出,待管道运行平稳后少量的水合物将逐渐分解。
此外,CO2流体含水量也是管道腐蚀控制的关键因素。确定经济合理的含水量设计值,对于海底CO2管道安全输送至关重要。目前,同时考虑CO2水合物形成与管道腐蚀的CO2含水量控制准则研究未见报道,杂质气体对不饱和含水条件下CO2水合物形成的协同影响等研究也属稀缺。
部分研究表明,CO2水合物浆料输送也是一种潜在的海洋CO2管道输送方式,与密相输送相比具有低能耗、低成本、无堵塞风险等优势,但固液两相输送可能面临冲刷腐蚀等潜在风险。
(二) 沿程腐蚀风险评估、监测及预警
海底CO2管道运行过程中不可避免地出现水汽凝结、游离水聚集、偶发性水段塞过流等问题,从而引发管道内壁腐蚀。在低温、高压环境中,CO2溶于水形成碳酸,碳钢管道难以耐受低pH值(< 3)电解质的长期浸蚀,成为海底CO2管道腐蚀穿孔的重要诱因。
1. 低温、高压CO2管道腐蚀风险评估
当存在游离水时,管道腐蚀风险主要取决于表面腐蚀产物膜的保护能力。在海底管道低温、高压工况下,FeCO3的临界饱和度关于温度敏感,因而保护性不佳;水气段塞等复杂流动可能对FeCO3膜造成冲刷腐蚀并破坏其完整性。一旦失去腐蚀产物膜的保护,碳钢在CO2饱和水溶液中将发生剧烈的活性溶解。当不存在游离水时,管道内沉积的水滴或薄液膜成为电化学腐蚀发生的电解质场所,相应腐蚀风险与CO2流体的含水量和流速相关。杂质气体会改变CO2流体特性,进而促成液滴沉降或改变腐蚀产物,在一定程度上加剧腐蚀。
在气、水交替注入工况下,管道内壁处于密相CO2和水相的周期性交替作用环境中。对于CO2相取代水相的过程,滞留水膜的停留时间直接决定管道腐蚀风险。粗糙或带有腐蚀产物的管道内壁容易滞留更厚的水膜,而干燥程度更高、输送速度更快的CO2流体有利于缩短水膜停留时间。
腐蚀是金属表面发生的电化学反应,只有在表面形成宏观或微观的电解质聚集(即游离水、水滴、水膜),腐蚀才能发生。在海洋CO2输送工况下,当管道所处水深为数百米,管道流体的温度和压力将处于CO2水合物形成区间;管道内的游离水将以水合物形式存在,微液滴或薄液膜也转变为固态水合物,无法提供电化学反应所需的电解质溶液。这种水合物形成环境中的管道腐蚀风险尚需进一步的实验验证。
2. 海底管道内腐蚀监测技术
CO2海底管道为整体焊接的封闭结构,在线监测腐蚀的难度较大。实际工程中集成运用多种技术,发挥CO2流体监控、局部监测、定期全覆盖检测的优势,辅以清管作业等措施、数字孪生等技术,实现多源数据融合和全生命周期评价。
现有的CO2管道工程均设置了含水量监测系统,用于实时记录CO2流体的含水量。当含水量高于设定的临界值时,需要启动干预措施以干燥CO2流体,确保管道系统稳定运行。
安装于特定位置的腐蚀探头或传感器(分为电阻型、电感型、电化学型等种类),可进行腐蚀信号监测并实时获取相关信息。这是一种局域性的腐蚀监测技术,在安装位置受限的海底环境中难以针对腐蚀风险点进行全流程周密布局,可能漏失大多数腐蚀监测的关键信息。
腐蚀缺陷检测是基于多种物理信号反馈的全覆盖式管道监测手段,分为超声法、涡流法、漏磁法等。在水下环境中,此类监测装备需要配合水下或管道机器人进行管道沿程扫描,但成本高昂。在清管器上搭载智能检测系统,可以获得更多管道内壁的腐蚀信息。对于海底CO2管道,超远距离作业和高压CO2对橡胶的溶解作用导致运行清管作业存在较大的技术挑战。
(三) CO2泄漏实时监测技术
海底管道运行环境复杂,加之泄漏点难以预见,实时监测并定位管道泄漏的难度极大。当泄漏事件发生后,首先需要借助在线监测系统的数据分析来获取泄漏点的大概位置,再利用水下机器人对事故点附近进行巡航检测,进而经由影像、声学等手段准确定位泄漏点,随后快速处置以将环境影响降至最低。
1. 分布式光纤定位技术
光纤传感技术是利用光纤光栅响应周围环境以获得光散射信号的变化,进而准确定位信号突变部位的一种原位监测技术。环境的应力、温度、振动等信号变化,均会对局域光纤内光信号的散射产生影响。该技术在长距离油气管道、输水管道等工程中已有应用,在海底管道健康监测方面也有少量案例。根据实践经验,百余千米长度管道的监测定位精度可达30 m;较短距离管道的监测定位精度可达1 m。
光纤传感器需要与海底管道同步(近距离)铺设,或紧贴于管壁外侧。海底CO2管道一旦发生局部泄漏,释放的高压CO2对局部环境产生降温、振动等多重作用,均会在光纤传感信号中得以体现。相较油气管道,CO2泄漏导致的温度变化更为显著,有利于光纤传感信号的准确识别。
利用分布式光纤传感技术,还可获得管道外壁的热流、微振动等信号。设置相应的信号阈值,可判断出管道内部水合物、水游离水、段塞流等的发生部位,为现场管理及安全预警提供可靠依据。考虑到深海环境下安装难度大、维护成本高,分布式光纤传感技术应用于海底管道泄漏定位还需克服具体施工问题。
2. 泄漏特征波谱定位技术
泄漏点处的CO2流体在管道内外压差作用下形成湍流,剧烈摩擦产生声波信号,声波将沿着流体和管壁传播。通过次声波达到两个监测点的时间差可计算出泄漏点位置并实现定位。次声波有着较短的波长,在传播过程中不易衰减,最大传播距离可达50 km,适用于海底管道长距离泄漏监测。根据陆上油气管道的运行经验,次声波法泄漏点定位精度可达±50 m。由于次声波作用距离远,一定长度的管道仅需在首 / 末段安装检测设备即可实现全程泄漏的监测与定位,因而具有广阔的应用前景。
负压波法、压力梯度法也是海底油气管道泄漏监测与定位的常用方法。对于海底密相输送CO2流体,泄漏发生后短时间内管道内压力变化较微弱,此类基于压力敏感的定位方法可能不适用于CO2管道泄漏监测。
3. 水下机器人巡检
水下机器人(ROV)是承担海底管道泄漏精准定位任务的关键装备。在经由光谱法、波谱法获得管道泄漏事件的初步定位信息后,需要ROV对可疑区段进行沿线巡检;利用ROV搭载的声学、光学、温度等传感器,获得管道泄漏的定量信息。ROV工作需要潜航器或维修船配合,联合完成海底管道的巡检和维修工作。以目前的技术能力看,ROV可执行4000 m深水作业。
近年来,自主水下航行器(AUV)正在快速发展,以适应恶劣海洋环境下的无人操控需求。尚处于实验室研发阶段的长期驻守自充电AUV在海底管道检测、定位与维修等方面展现出广阔前景。与人工智能技术结合,AUV可适时自主开展常规巡检任务,获取信息并同步传输至终端控制平台,等待人为指令开展必要的维修前准备工作;将缓解海底管道巡检的人力资源需求,适应极端环境下海底管道泄漏事故的快速定位与高效处置场景。
(四) 高压CO2泄放及对环境的影响
海底CO2泄漏将引发一系列的海洋安全与环境问题。面向突发性的海底CO2管道泄漏事故,需要认清CO2泄放规律,准确把握泄漏过程的关键因素并客观评价对环境的影响后果,才能实施应急救援并开展后续生态补偿等工作。
1. 海底管道CO2泄放规律
理解海底管道高压密相CO2的泄放过程,需从两方面出发:CO2羽流在海水中的逸散规律,CO2泄放过程中管道内流体的相变规律。
与陆上CO2管道不同,海底管道泄放出的高压CO2羽流会受周围海水限制,其逸散规律与水深密切相关。理论研究认为,高压海水环境可有效抑制CO2逸散。如果泄放点浅于10 m水深,超过90%的CO2将以气体形式快速释放到海平面以上的大气中。如果泄放点深于50 m水深,则全部CO2气体被溶解于海水,在海平面几乎观察不到气泡逸出。如果泄放点深于500 m水深,CO2将以液态形式涌出,随后在较短时间内溶解于深层海水。如果泄放点深于1000 m水深,CO2与海水形成水合物,可能影响泄放速率甚至间歇性堵塞泄放口。
在海底管道CO2泄放过程中,管道内部流体的温度和压力会发生变化,可能导致气液两相流动,局部低温则进一步增加管道材料脆性断裂的风险。国内外分别开展了不同规模的现场管道、模拟实验管道的测试研究。长度为50 km、管径为0.6 m的陆上埋地管道中9300 t CO2泄放实验表明,泄放过程中的温度、压力沿着气液分界线演变,管道内出现了气液两相共存。小规模的CO2管泄放模拟中,监测到CO2流体的气液两相共存状态,观察到干冰直接喷出现象。海洋CO2管道不设置隔离阀门或分段节流阀,如果某处发生泄漏,则整条管道中CO2均参与泄放,尚无直接相关的实验研究。
2. 海底管道CO2泄漏的安全、环境与生态影响
CO2虽然无毒性,但易于在地表或海面聚集,可能对附近人员或生物造成窒息、冷冻等安全伤害。1994—2013年,北美地区陆上CO2管道累计发生64次泄漏事件,虽未造成严重的伤亡事故,但需要清醒认识CO2泄漏的潜在安全隐患。例如,1986年喀麦隆的尼奥斯湖底的天然CO2大规模喷发,在短时间内蔓延至周边的低谷地带,造成1700余人死亡。CO2管道中的其他杂质气体如H2S、SO2等,在泄漏过程中也会严重威胁人身安全。也要注意到,海洋表面的人员聚集度非常低,加之高压海水可溶解并缓冲CO2羽流,一般认为海底管道CO2泄漏的安全风险远低于陆上管道,对海面船只、平台上的工作人员影响有限。
大量泄漏的CO2溶解于海水,会降低局部区域海水的pH值,短时间内对海洋浮游生物造成直接伤害。长期生活于低pH值环境中的海洋生物,其生活习性、细胞内环境会发生改变。也要注意到,与CO2地层泄漏不同,CO2管道泄漏更加局域化,更容易实施人为管控措施,相应影响强度低、时间短;当CO2管道得到修复,所引发的负面环境生态效应也随之消失。
(五) 海洋CO2管道输送面临的工艺技术挑战
1. 低温、高压环境中CO2含水量阈值设置缺乏依据
海底管道中CO2含水量控制需要考虑腐蚀、水合物形成两方面因素。工程上最简单的做法是将CO2脱水处理,使含水量远低于相应环境的含水饱和度。国外工程经验是将管道输送的CO2含水量控制在摩尔比< 5×10-4,但缺少充分的科学论证。在Weyburn油田、Snøhvit项目中,选择了数值更低、更为安全的含水量阈值,然而CO2脱水处理成本昂贵,杂质气体则进一步恶化输送环境。平衡含水量、流动安全之间的关系,成为大规模CO2管道输送的关键技术难题。
2. 海底CO2管道腐蚀风险评估与监测技术
CO2管道腐蚀与游离水存积相关,发生的时间和空间均受局域环境波动、管道几何等因素的影响,具有较大的不确定性。常规的全覆盖式腐蚀监测技术不具备时效性,当发现管道腐蚀缺陷时往往破坏已无法逆转。局部腐蚀实时监测技术仅安装于特定位置,存在监测信息代表性差、腐蚀风险估计不足的问题。海底CO2管道沿程腐蚀风险评估的核心难题是融合可获取的流体、环境、材料等多类型参数,形成“流动‒管道‒材料”集成的理论预测模型和风险识别方法。
3. 超远距离高压CO2管道清管技术
清管作业常用于管道检测、清除堵塞物,是管道运行的重要保障措施。在Weyburn油田、美国NJED项目中,执行了CO2管道全线或支线的清管作业,用于检测管道腐蚀和排出游离水。在长距离CO2输送(>50 km)过程中,清管作业面临着代表性难题:清管器主要依靠流体压力运行,超远距离清管作业的压力损失可能导致清管器动力不足,从而存在滞留风险;在密相或超临界CO2环境中,超远距离作业时清管器的密封部件会发生磨损或降解而失效。
4. 低成本海底CO2管道泄漏精准定位技术
次声波法用于泄漏定位虽然成本低、沿线装备少,但定位精度受作业环境影响较大,也仅适用于距离不超过50 km的海底管道(或需要分段监测),才能确保精度和适用性。分布式光纤传感技术被视为CO2海底管道泄漏快速精准定位的先进方向,但光缆需要伴随海底管道同步铺设,施工难度大、成本高。此外,光纤传感器仅能监测光缆铺设一侧的CO2泄漏信号,若进行管道空间全方位监测,需要围绕管道至少布设4个象限的电缆,将显著增加工程投资。因而提高定位精度、降低工程成本是当前技术攻关的重点方向,集成多种实时监测与沿程动态模拟技术能够更好实现全方位的快速精准定位。
来源:海洋CO2管道输送技术现状与展望[J].中国工程科学